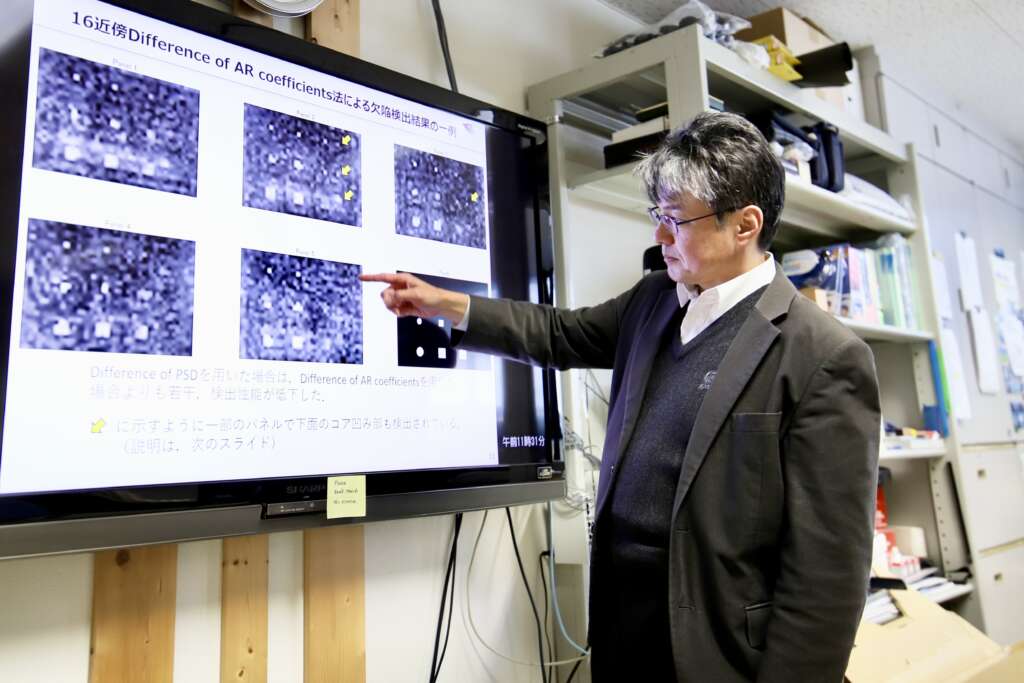
工学部電気電子・情報工学科 情報コース
教授横田 康成
データサイエンスによる数値の可視化で、リスク削減と効率化を図る
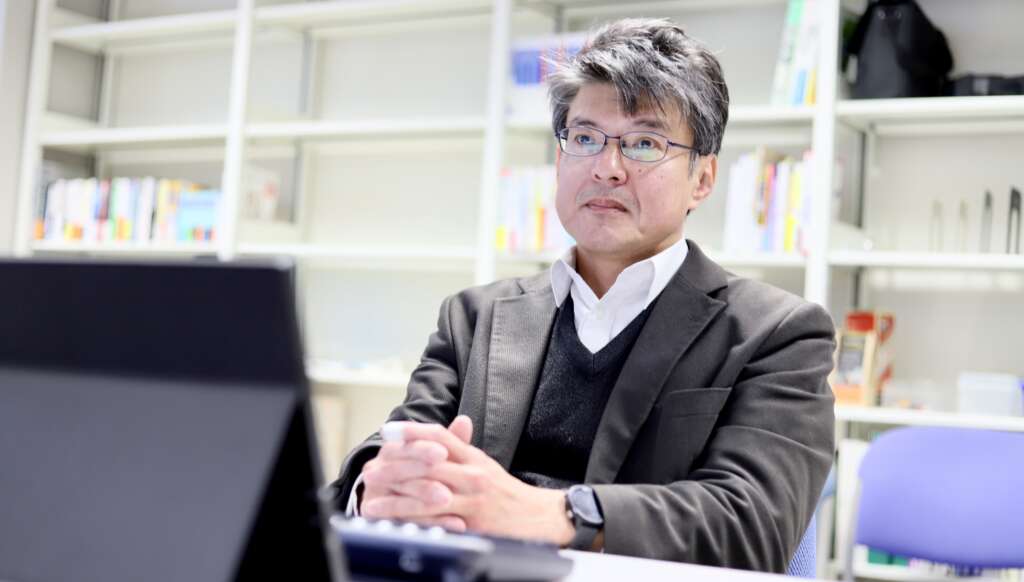
日本の航空機産業の実情
本研究では、私の専門分野の一つである「データサイエンス」を武器に、航空機製造における工場内のリスクの軽減と効率化を目指して“生産管理”と“品質管理”の新しい方法を開発しようとしています。
データサイエンスというと、AIや機械学習を連想する方も多いのですが、基本は数理統計学であり、実際に記録された膨大な量の工程実績データを計算機の力を借りて分析することにより、
工場内の製品の動きを見える化し、数日先の工場の様々な状態を予測可能にします。
自動車の工場などでは、自動車の原型が次々とベルトコンベアで移動し、その周りをロボットアームや人が取り囲み、順番に様々な部品を取り付けてゆくといった機械化、
効率化された印象があります。自動車よりもはるかに高性能かつ高価格な航空機の工場では、さぞかし、さらに最先端な技術が取り入れられている印象があります。しかし実際は、職人の熟練の技が鍵を握る、超アナログ的な製造現場となっています。
航空機の工場では、“多品種”の部品から“少数”の航空機を作るため、“多品種少量生産”と呼ばれています。その生産工程は、大きく多品種の部品の製造工程、
それらから航空機の一部分を組み立てる工程、さらにそれらを統合して一機の航空機に仕上げる工程があります。航空機部品の製造工場の構成は、
製造に必要な工程毎に区分けされており、製品は製造に必要な工程作業エリア(ジョブショップ)を回ります。ある部品が必要な場合には、
それを作るオーダーが発行されて原材料が投入されたのち、複数のジョブショップをめぐって順次、加工や検査を繰り返すことにより部品が製造されます。こうした生産を「ジョブショップ型生産」といいます。
部品数やジョブショップの数、オーダー数が膨大であるため、毎日のオーダーの状況を把握することやオーダーの完了日を正確に予測することが非常に困難です。
一方で、在庫切れは組み立て工程に影響を与えるため絶対に避けなければなりません。そこで、現状はオーダーを必要以上に早めに発行し、結果的に大量の在庫を抱え、コスト増の要因となっています。
そこで、いつオーダーを投入したらいつ完了するのかを正確に予測できるようにすることが当面の目標ですが、そのためには、すべての各ジョブショップにおいて、
そのジョブショップでのオーダー処理の仕組みを調べ上げて、オーダーを処理するためにかかる日数を割り出し、それらを工場全体で積み上げてゆく製造原理に基づいた方法と、
製造原理にはあまり深く踏み込まずに、過去の膨大な工程実績データから原因と結果の関係を数理的に解析してゆくデータサイエンス的アプローチがあります。本研究では後者のアプローチをとっています。
こうしたオーダー完了日の正確な予測が可能になれば、在庫切れのリスクを下げつつ、在庫量を最小にするようなオーダー発行計画を立てることが可能になります。
また、オーダーの動きをシミュレーションすることが可能になるため、あるジョブショップの機能が停止するなどのトラブルがあった際には、今後のオーダーの流れを
予測することが可能になり、その結果、在庫切れが予測される場合には、どのような現場介入をしたらよいかを再計画し、直ちに工場を正常状態に戻すことが可能になります。
新幹線の運行管理室では、すべての新幹線の位置や速度をモニタリングでき、トラブル発生時には、迅速な復旧に向けて、新たな運行スケジュールを再計画し、
新幹線の運行を制御する司令塔になります。これと同じように、将来的には、工場内にオーダー運行管理室を設置し、すべてのジョブショップの状態、
オーダーの動きを統合的にモニタリングし、トラブルの予測と防止、トラブル発生時には新たな生産スケジュールを再計画できるような生産管理が行われるようになるとよいと思っています。
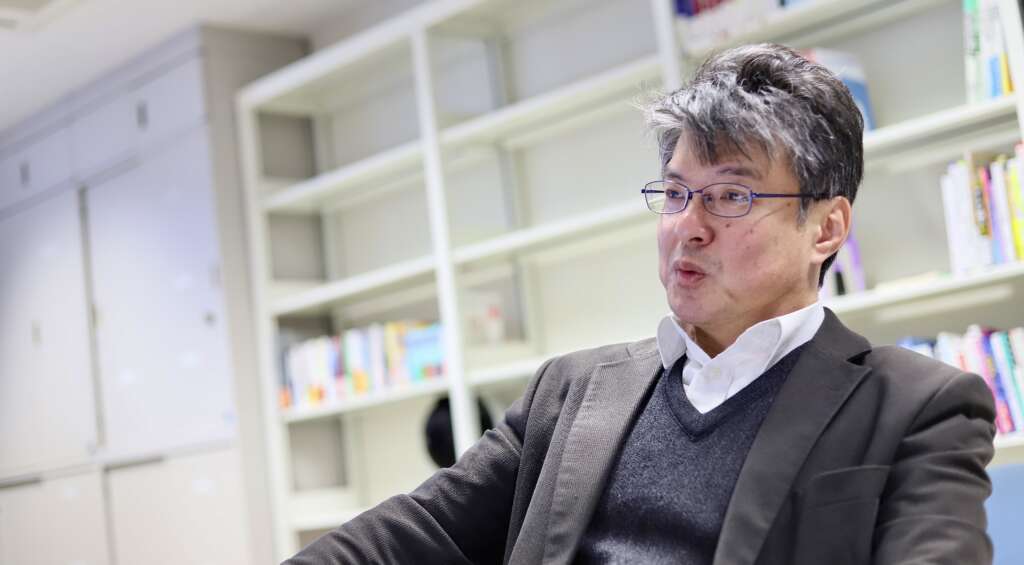
サイバー空間を活用したフィジカル空間への実用化
航空宇宙生産技術開発センターには、「サイバー空間」、「フィジカル空間」という考え方があります。
いろいろなスケールで解釈することができますが、例えば、「フィジカル空間」が工場など現実の世界、「サイバー空間」が主に計算機内でシミュレーションにより実現される仮想空間を表します。
航空機製造産業では、小さな部品一つ一つの製造方法から検査方法まで細かく方法が管理されています。新しい方法を導入するためには、
それにより品質が低下しないかなどの審査を受けて合格する必要があります。こうしたこともあって最先端の航空機製造産業であっても、
最新の製造技術を導入しにくい保守的となる要因になっています。そのため、先ほどお話したように、たとえ新しい優れた生産管理の仕組みを考案したとしても、
直ちに実際の工場である「フィジカル空間」に導入することはできません。万が一にでも部品の品質低下を招き航空機事故の要因になったら取り返しがつきません。
しかし、「サイバー空間」では、いくら失敗しても良いのです。計算機は、疲れたり怒ったりしません。「サイバー空間」で十分にトライ&エラーを繰り返し、
熟成させてから、「フィジカル空間」に転用すればよいのです。これが、センターが考えている「サイバー空間」と「フィジカル空間」の融合です。
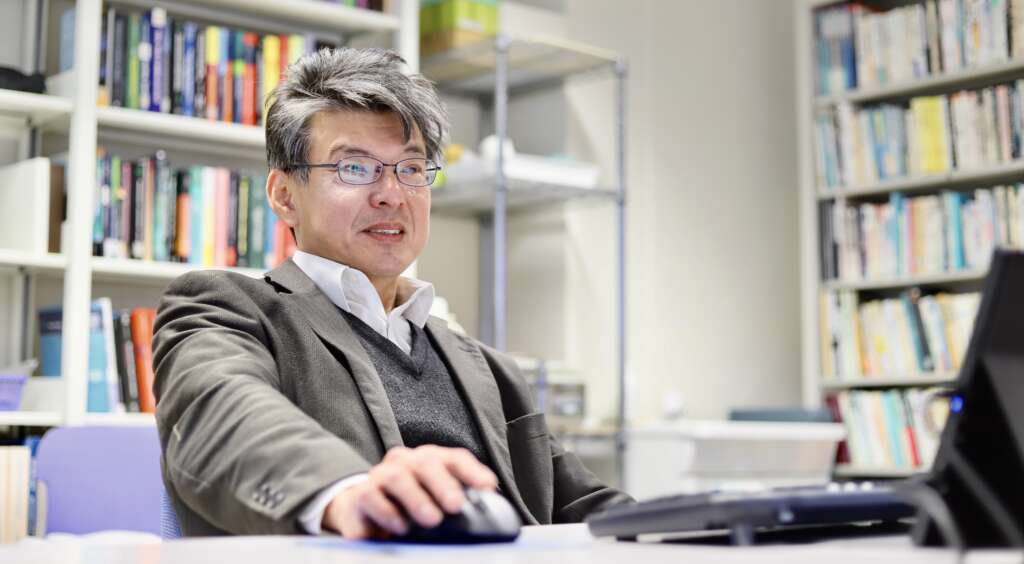
人間感覚のデメリットと機械化の導入のメリット
部品の“品質管理”に関しても非常に保守的です。例えば、ある部品の内部の欠陥の発見のために打音検査が用いられています。
これは、部品をハンマーで叩いた際の音を聞き、ある部分で異音がしたら内部に欠陥があるとする非破壊検査の一つです。
X線などを使えば容易に内部の欠陥は見つかるのですが、コストの問題か、X線による素材への悪影響の懸念か、導入されていません。
実際の検査は、資格を持った検査員が行うのですが、試しに私がやってみても、とても異音と分からない欠陥もあり、検査員の超人的な耳の良さに驚かされます。
人の能力のすばらしさでもあるのですが、一方で、トレーサビリティもないし、定期的に検査員の聴力テストは行っているとは思うものの年を取って耳が遠く
なったらどうするのか、こんな品質検査で良いのかと思ってしまいます。
そこで、本研究では、検査対象の各点を叩いた打音を計算機で分析することにより、周辺と打音の音色が異なる領域をマップとして示す方法を開発しています。
現状でも、少なくとも私よりは異音を聞き分ける能力の高い方法が完成しています。先ほど申したように航空機製造産業では、新しい方法の導入は非常に難しいので、
これを直ちに検査員による打音検査の代わりにはできませんが、まずは、検査員による検査結果を補強するため、あるいは検査員による検査の前に提示することにより、検査員の負担を低減できないかと考えています。
自動化、機械化によって人間の負担を減らす事で、作業効率や安全性を高めていく事が出来、日本の航空産業はより良いものになるはずです。
これらのように航空機の生産現場は,様々な専門分野がかけ合わさって成り立っています。
この航空宇宙生産技術開発センターが仲介役となって、バラバラになっている各研究室の研究テーマを、テーマによってマッチングさせることにより,より良い航空機づくりに繋げていってほしいですね。
別の分野との研究を掛け合わせる事により、大きな相乗効果を生み出せると思います。